24 kinds of metal materials commonly used in mold processing and their characteristics
There are more than a hundred kinds of materials that can be used for mold processing, including metal, plastic, inorganic nonmetal and paraffin, etc. However, according to the actual needs, the uses and demands of each material are different. Today, let’s talk about the most commonly used 24 kinds of metal materials in mold processing.
1. 45โโ High-quality carbon structural steel is the most commonly used medium carbon quenched and tempered steel.
Main features: Medium carbon quenched and tempered steel is the most commonly used steel, with good comprehensive mechanical properties, low hardenability, and easy to crack when quenched by water. Small pieces should be tempered, and large pieces should be normalized.
Application: It is mainly used to manufacture moving parts with high strength, such as turbine impeller, compressor piston, shaft, gear, rack and worm, etc. Pay attention to preheating before welding and annealing after welding.
2. Q235A(A3 steel)-the most commonly used carbon structural steel
Features: High plasticity, toughness, welding performance, cold stamping performance, certain strength and good cold bending performance.
Application: Widely used in parts and welding structures with general requirements. Such as pull rods, connecting rods, pins, shafts, screws, nuts, ferrules, brackets, stands, building structures and bridges, etc.
3. 40Cr-one of the most widely used steel grades, which belongs to alloy structural steel.
Features: After quenching and tempering, it has good comprehensive mechanical properties, low-temperature impact toughness, low notch sensitivity, good hardenability, high fatigue strength when oil is cooled, and cracks easily occur when water is cooled. The cold bending plasticity is moderate, and the machinability is good after tempering or quenching and tempering, but the weldability is not good, so it is easy to produce cracks. Before welding, it should be preheated to 100โ ~ 150โ, which is generally used in quenching and tempering state. Carburizing and high-frequency surface quenching can also be carried out.
Examples: After quenching and tempering, it is used to manufacture medium-speed and medium-load parts, such as machine tool gears, shafts, worms, spline shafts and thimble sleeves, etc. After high-frequency surface quenching, it is used to manufacture parts with high hardness and wear resistance, such as gears, shafts, spindles, crankshafts, mandrels, sleeves, pins, connecting rods, screws and nuts, intake valves, etc. After quenching and tempering at medium temperature, it is used to manufacture heavy-duty and medium-speed impact parts, such as oil pump rotor, slider, gear, spindle and collar, etc. After quenching and low-temperature tempering, it is used to manufacture heavy-duty, low-impact and wear-resistant parts, such as worm, spindle, shaft and collar, etc. After carbonitriding treatment, drive parts with large size and high low-temperature impact toughness, such as shafts and gears, are manufactured.
4. HT150-gray cast iron
Examples: gear box, machine tool bed, box, hydraulic cylinder, pump body, valve body, flywheel, cylinder head, pulley and bearing cover, etc.
5. 35โโ Common materials of various standard parts and fasteners
Main features: appropriate strength, good plasticity, high cold plasticity and acceptable weldability. Under cold condition, local upsetting and wire drawing can be performed. Low hardenability, use after normalizing or tempering.
Application: It is suitable for manufacturing parts with small cross-section and large load, such as crankshafts, levers, connecting rods, shackles, various standard parts and fasteners.
6, 65mn-commonly used spring steel
Examples: small-sized flat and round springs, cushion springs, spring springs, spring rings, valve springs, clutch reeds, brake springs, cold coil springs, clamp springs, etc.
7, 0cr18ni9-the most commonly used stainless steel (American steel grade 304, Japanese steel grade SUS304)
Characteristics and applications: As stainless heat-resistant steel, it is most widely used, such as food equipment, general chemical equipment, etc.
8. CR12-Commonly used cold-working die steel (American steel grade D3, Japanese steel grade SKD1)
Characteristics and application: Cr12 steel is a widely used cold-working die steel, belonging to high carbon and high chromium type ledeburite steel. The steel has good hardenability and good wear resistance. Because the carbon content of Cr12 steel is as high as 2.3%, its impact toughness is poor, brittle fracture is easy, and uneven eutectic carbide is easy to form. Because of its good wear resistance, Cr12 steel is mostly used to manufacture punch and die, drill sleeve, gauge, wire drawing die, pressing die, thread rolling plate, drawing die and cold pressing die for powder metallurgy, etc., which require low impact load and high wear resistance.
9. DC53-Commonly used cold-working die steel imported from Japan
Characteristics and applications: high-strength and toughness cold-working die steel, steel number of Datong Special Steel (plant) manufacturer in Japan. After tempering at high temperature, it has high hardness, high toughness and good wire cutting performance. Used for precision cold stamping die, drawing die, thread rolling die, cold blanking die and punch, etc.
10. dccr12mov-wear-resistant chromium steel
Compared with Cr12 steel, the carbon content of domestic steel is lower, and Mo and V are added, so that the unevenness of carbide is improved. Mo can reduce carbide segregation and improve hardenability, and V can refine grain and increase toughness. This steel has high hardenability, the cross section below 400mm can be completely hardened, and it can still maintain good hardness and wear resistance at 300~400โ. Compared with Cr12, it has higher toughness. The volume change during quenching is small. It also has high wear resistance and good comprehensive mechanical properties. Therefore, it is possible to manufacture various kinds of dies with large cross section, complex shape and large impact, such as common drawing dies, punching dies, stamping dies, blanking dies, trimming dies, rolling dies, wire drawing dies, cold extrusion dies, cold shearing scissors, circular saws, standard tools and measuring tools, etc.
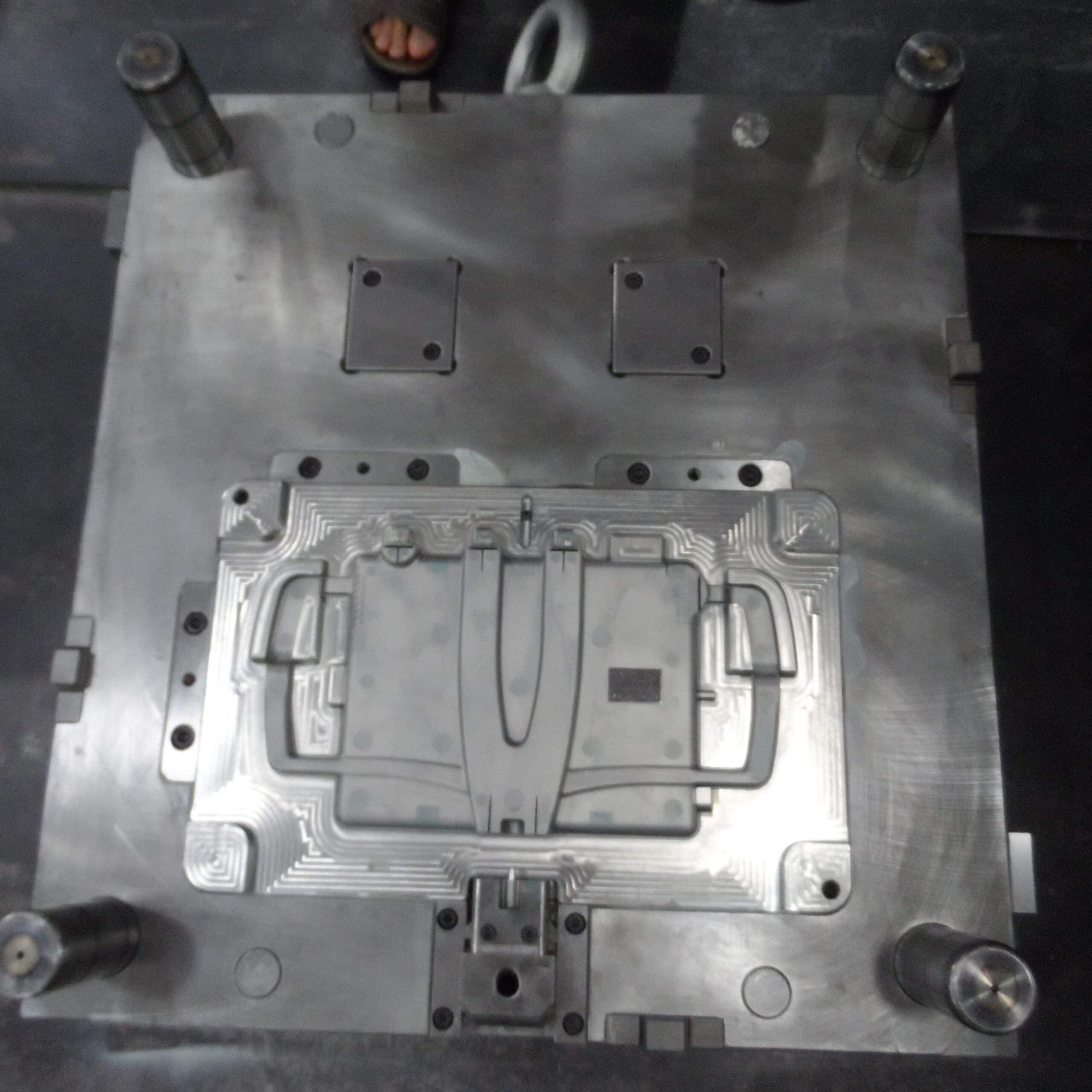
11. SKD11-Tough Chromium Steel
Produced by Hitachi, Japan. Technically, the casting structure in steel is improved, the grain size is refined, the toughness and wear resistance are improved compared with those of Cr12MoV, and the service life of the die is prolonged.
12. D2-high carbon and high chromium cold working steel
Made in America. It has high hardenability, hardening capacity, wear resistance, high-temperature oxidation resistance and good corrosion resistance after quenching and polishing. Heat treatment deformation is small. It is advisable to manufacture all kinds of cold working dies, tools and measuring tools that require high precision and long service life, such as drawing dies, cold extrusion dies and cold shearing knives.
13. SKD11 (SLD)-high chromium steel with no deformation and toughness
Produced by Hitachi, Japan. With the increase of Mo and V content in the steel, the casting structure in the steel is improved, the grain size is refined, and the carbide morphology is improved. Therefore, the strength and toughness (bending strength, deflection, impact toughness, etc.) of this steel are higher than those of SKD1 and D2, the wear resistance is also increased, and the tempering resistance is higher. Practice has proved that the service life of this steel die is longer than that of Cr12MoV. We often manufacture high-demand dies, such as drawing dies and dies that impact grinding wheels.
14. DC53-High toughness and high chromium steel
Produced by Japan Datong Co., Ltd. Heat treatment hardness is higher than SKD11. After tempering at high temperature (520 ~ 530โ), the hardness can reach 62~63HRC. In terms of strength and wear resistance, DC53 exceeds SKD11, and its toughness is twice that of SKD11. The toughness of DC53 rarely appears cracks and cracks in cold-working die manufacturing, which greatly improves the service life. The residual stress is small, and it can be reduced by turning back at high temperature. Because the cracks and deformation after WEDM are suppressed, the machinability and abrasiveness exceed SKD11, and it is used in precision stamping dies, cold forging dies and deep drawing dies.
15. SKH-9-Universal high-speed steel with high wear resistance and toughness.
Produced by Hitachi, Japan. Used for cold forging dies, slitting machines, drills, reamers and punches, etc.
16. ASP-23-Powder Metallurgy High Speed Steel
Made in Sweden. Carbide distribution is extremely uniform, wear-resistant, high toughness, easy processing and stable size after heat treatment. Used for punch, deep drawing die, drilling die, milling cutter, shearing blade and other cutting tools with long life.
17. P20โโ the size of plastic molds required in general.
Made in America. Electro-corrosive operation. Pre-hardened HB270~300, quenching hardness HRC52.
18, 718โโ Large and small plastic molds with high requirements
Made in Sweden. Electro-corrosive operation. The factory state is pre-hardened HB290~330, and the quenching hardness is HRC52.
19. nak80-high mirror surface and high precision plastic mold
Japan’s Datong Co., Ltd.. The factory state is pre-hardened HB370~400, and the quenching hardness is HRC52.
20. S136โโ Anti-corrosion and mirror-polished plastic mold
Made in Sweden. The factory pre-hardened HB is < 215, and the quenching hardness is HRC52.
21. H13-common die casting die
Used for aluminum, zinc, magnesium and alloy die casting, hot stamping die, aluminum extrusion die, etc.
22. SKD61-Advanced Die Casting Die
Produced by Hitachi, Japan. After electroslag remelting technology, the service life is obviously longer than H13. Used for hot stamping die and aluminum extrusion die.
23. 8407-Advanced Die Casting Die
Made in Sweden. Used for hot stamping die and aluminum extrusion die.
24. FDAC-sulfur is added to enhance its machinability.
Pre-hardness HRC38~42, which can be directly engraved without quenching and tempering. Used for small batch molds, simple molds, various resin products, sliding parts and mold parts with short delivery time. Such as zipper mold, spectacle frame mold, etc.