Analysis of color stripes and color lines of injection molded products
Although the color masterbatch coloring is better than dry powder coloring and dyeing paste coloring in terms of color stability, color purity and color migration, the distribution, i.e., color particles in diluted plastic in the mixing uniformity is relatively poor, and the finished products naturally have regional color differences. Main solutions.
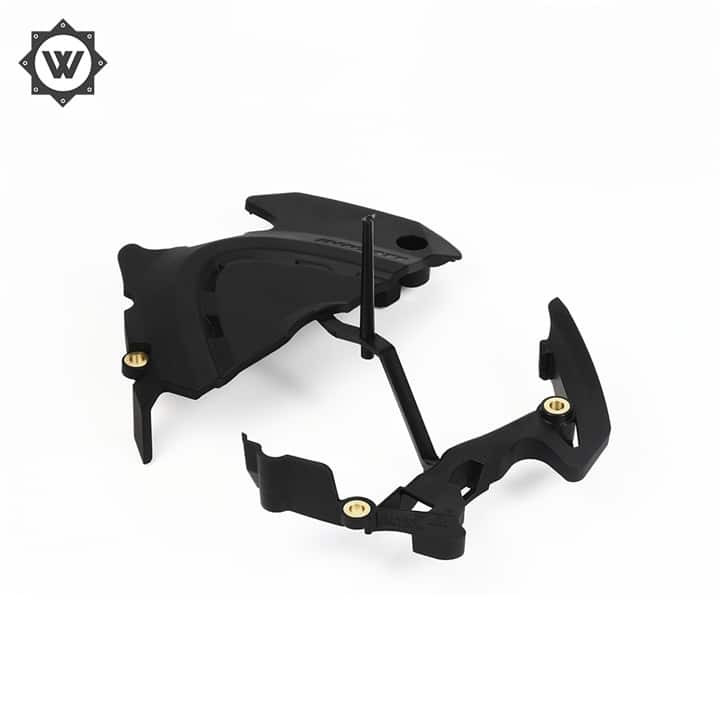
(1) increase the temperature of the filling section, especially the temperature of the back end of the filling section, so that its temperature is close to or slightly higher than the temperature of the melting section, so that the color masterbatch into the melting section as soon as possible to melt, promote and dilute uniform mixing, increase the opportunity of liquid mixing.
(2) Under the condition of certain screw speed, increase the back pressure to make the temperature of the molten material in the barrel and the shearing effect are improved.
(3) Modify the mold, especially the pouring system, such as the gate is too wide, when the molten material through, turbulent flow effect is poor, the temperature is not high, so it is not uniform, ribbon mold cavity, should be changed to narrow.