Application Advantages of High Speed Machining Process for Automobile Dies
High speed cutting is the development trend of automobile die manufacturing
High speed machining technology is an advanced manufacturing technology in the 21st century, which has strong vitality and broad application prospects. High speed machining technology can solve a series of problems that have been perplexed in the conventional machining of automobile dies. In recent years, in the United States, Germany, Japan and other industrial developed countries, high-speed cutting technology has been widely used in most mold companies, and about 85% of mold EDM processes have been replaced by high-speed machining. High speed machining technology, which combines high efficiency, high quality and low consumption, has become the mainstream in the international mold manufacturing process.
Through the practice and application of high-speed cutting technology in automobile die manufacturing industry at home and abroad, high-speed cutting technology has the following advantages:
1、 High speed cutting improves processing speed
High speed machining is used to machine automobile dies at a cutting speed about 10 times higher than that of conventional machining. Since the excitation frequency of the spindle of high-speed machine tool is far beyond the natural frequency range of the “machine tool workpiece” system, the processing of automobile dies is stable and impact free.
2、 High production efficiency of high-speed cutting
Using a high-speed machining center or a high-speed milling machine to process the mold, the rough and finish machining of the mold surface and the machining of other parts of the automobile mold can be completed in one clamping of the workpiece, which is the so-called “One Pass Machining” technology. The application of high speed machining technology has greatly improved the development speed of automobile dies.
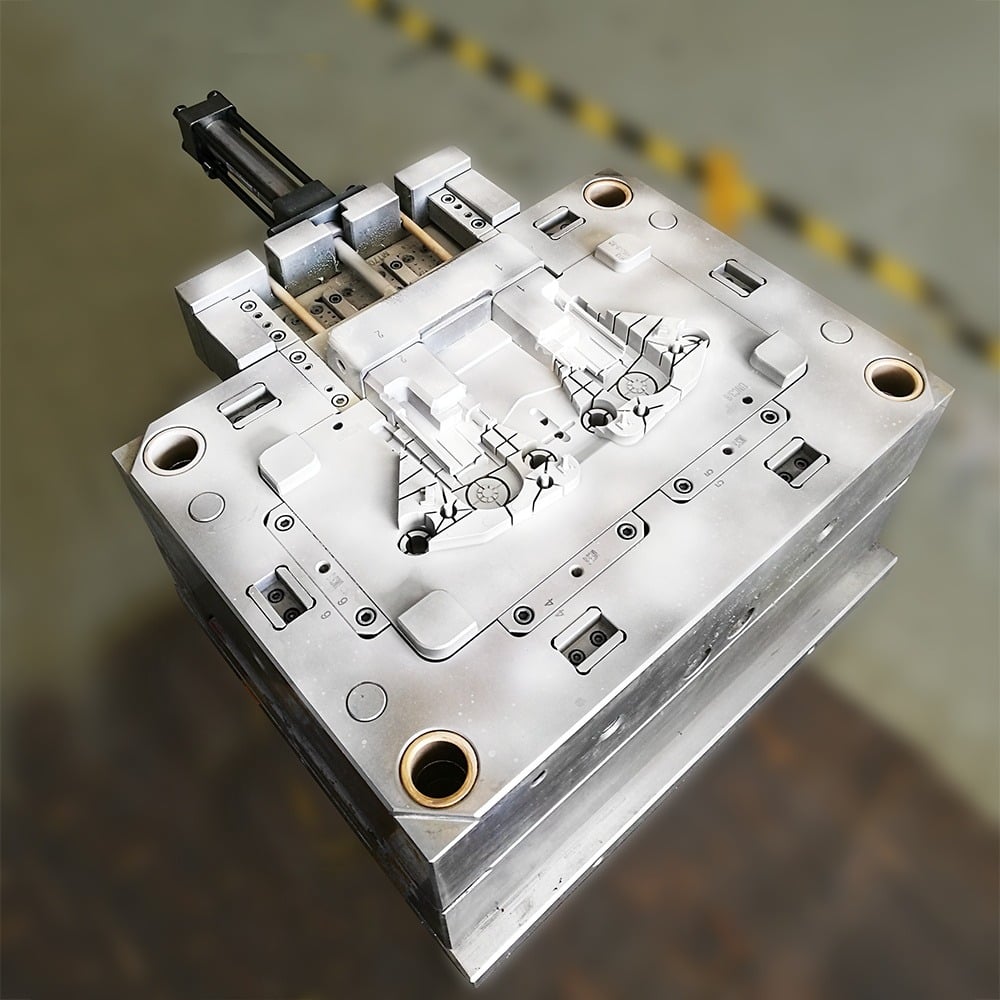
3、 High speed machining can obtain high-quality machined surface
Because of the extremely small step distance and cutting depth, high speed cutting can obtain high surface quality, and even eliminate the process of bench worker finishing.
4、 Simplify processing procedures
Conventional milling can only be carried out before quenching, and the deformation caused by quenching must be manually trimmed or finally formed by electric machining. Now it can be completed by high-speed cutting, and there is no case hardening caused by electric machining. In addition, because the cutting amount is reduced, high-speed machining can use tools with smaller diameters to process smaller fillet radii and mold details, saving some machining or manual finishing processes, thus shortening the production cycle.
5、 High speed machining makes the repair process of automobile dies more convenient
Automobile dies often need to be repaired for many times in the process of use to extend their service life. If high-speed cutting is used, the work can be completed faster, and the machining effect of replacing grinding with milling can be achieved. In addition, the original NC program can be used, without re programming, and can be accurate.
6、 High speed machining of hard automobile die with complex shape
It can be seen from the high-speed cutting mechanism that the cutting force is greatly reduced during high-speed cutting, and the cutting process becomes easier. High speed cutting has great advantages in cutting high-strength and high hardness materials. It can process automobile dies with complex surfaces and high hardness.