Calculation method of working dimensions of injection molded parts
The working dimensions of injection molded parts are the dimensions of the molded parts directly used to form the plastic parts, mainly the radial dimensions of the cavity and the core, the depth dimensions of the cavity and the height dimensions of the core, the location dimensions between the core and the core, etc. Any plastic parts have certain geometric shape and size requirements, such as in use with the required size, the accuracy requirements are higher. In the mold design, the working size and accuracy level of molded parts should be determined according to the size and accuracy level of plastic parts. The factors affecting the dimensional accuracy of plastic parts are quite complex, and these influencing factors should be used as the basis for determining the working size of molded parts for injection molding process. The main factors affecting the dimensional accuracy of plastic parts are as follows.
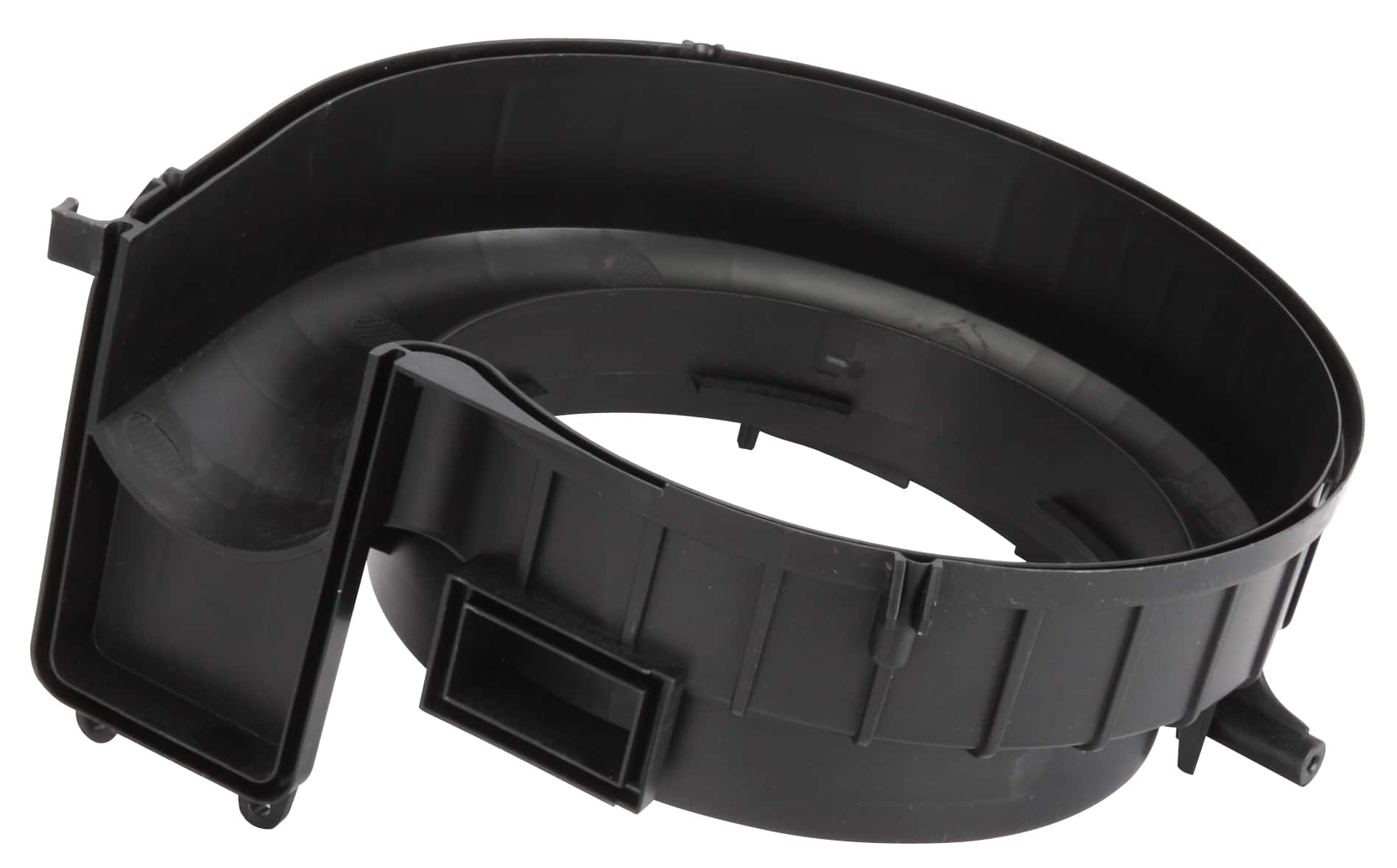
(1) the impact of shrinkage of plastic parts: the shrinkage of plastic parts after molding is related to the variety of plastic, the shape, size and wall thickness of plastic parts, the structure of the mold, the process conditions of molding and other factors. In mold design, it is difficult to determine the exact shrinkage rate, because the selected calculated shrinkage rate and the actual shrinkage rate are different. Changes in process conditions and plastic lot numbers during the production of plastic parts can also cause fluctuations in the shrinkage rate of plastic parts. The deviation and fluctuation of shrinkage rate will cause the dimensional error of plastic parts.
(2) mold molding parts manufacturing errors: mold molding parts manufacturing accuracy is one of the important factors affecting the size accuracy of plastic parts. The lower the accuracy of molding parts injection processing, the lower the dimensional accuracy of molded plastic parts. Practice shows that the tolerance accounts for 1/3 of the total tolerance of plastic parts low, this in determining the working size tolerance value of molded parts can be 13 1/4 of the tolerance of plastic parts, or take IT7 ~ IT8 as mold manufacturing tolerance. The manufacturing tolerance of the cavity or core should be determined according to the dimensional chain when demoulding and plastic combination.
(3) mold molding parts wear: mold in the process of use, due to the plastic melt flow of scouring, pieces of friction, molding process may produce corrosive gas corrosion, and due to the above reasons caused by the molding parts surface roughness value increases and re-polishing polishing, etc., are caused by changes in the size of the molding parts, this change is called molding parts wear. The result of wear is that the cavity size becomes larger and the core size becomes smaller. Wear size is also related to the variety of plastic and mold materials and heat treatment. The above-mentioned factors are the main frictional wear of the molded parts during demolding, for the sake of simplifying the calculation, where the molded parts surface perpendicular to the direction of demolding, can not be considered wear; and the molded parts surface parallel to the direction of demolding, should be considered wear.
When calculating the working size of injection molding parts, the amount of wear should be determined according to the output of plastic parts, plastic varieties, mold materials and other factors. The production batch is small, the wear amount to take small values, or even can not consider the amount of wear; glass fiber and other reinforced plastics on the molding parts wear serious, the wear amount can be large values; friction factor is small thermoplastics on the molding parts wear small, the wear amount can be small values; mold material wear resistance, surface chromium plating, nitriding treatment, the wear amount can be small values. For small and medium-sized plastic parts, the amount of wear can be 1/6 of the tolerance of the plastic parts; for large plastic parts should be taken below 1/6.
(4) mold installation with the error: mold molding parts assembly error and molding parts in the molding process with the change of clearance, will cause changes in the size of the plastic parts. For example, due to the molding pressure so that the mold parting surface has a tendency to expand, and at the same time, due to the residue on the parting surface or the influence of the flatness of the template injection molding process, there is a certain gap on the parting surface of the dynamic mold, which has an impact on the height direction of the plastic injection molding process size; movable core and template with too much clearance will affect the accuracy of the position of the hole on the plastic part.
To sum up, the dimensional error of the plastic part in the injection molding process should be the sum of the above-mentioned errors. It can be seen that the dimensional accuracy of the plastic part is often low due to the many influencing factors and the large accumulated errors. When designing plastic parts, the selection of its dimensional accuracy should not only consider the use and assembly requirements of plastic parts, but also consider the possible errors generated by plastic parts in the molding process, so that the tolerance value Δ specified for plastic parts is greater than or equal to the cumulative error caused by the above factors, that is, when designing, consideration should be given to make the cumulative error caused by the above factors not exceed the tolerance value specified for plastic parts, in general, the fluctuation of shrinkage rate In general, the fluctuation of shrinkage rate, mold manufacturing tolerance and molding parts wear is the main reason to affect the dimensional accuracy of plastic parts. Moreover, not all dimensions of a plastic part are related to the above factors, and it is very unlikely that all errors will be biased towards large values or small values at the same time.
The dimensional errors caused by fluctuations in shrinkage increase as the size of the part increases. Therefore, the production of large plastic parts, due to shrinkage rate fluctuations on the shape of the part tolerance can be wrong single often improve the mold manufacturing to improve the accuracy of the parts is difficult and uneconomical, should be stable molding, choose shrinkage rate fluctuations in the smaller plastic. When producing small plastic parts, mold manufacturing tolerances and molding parts wear, is the main factor affecting the dimensional accuracy of plastic parts, therefore, should improve the mold accuracy level and reduce wear.
Calculation of the working size of molded parts for injection molding process must consider the formula for calculating the working size of molded parts when plastic shrinkage rate is considered. If other factors are considered, the formula for calculating the working dimensions of molded parts has different forms.