Features of insert molding injection molding process
Insert molding refers to the molding process in which the mold is filled with pre-prepared inserts of different materials and then injected with resin, and the molten materials are joined with the inserts and cured to make products. Injection molding on the substrate refers to the method of insert molding on the local surface of the metal plate.
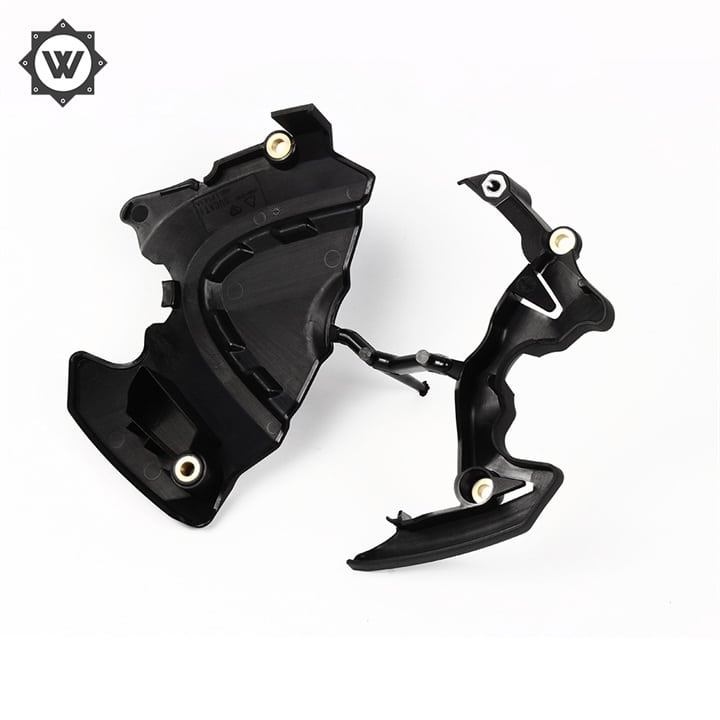
Its characteristics are as follows.
1、The combination of the ease of molding and bending of resin and the rigidity, strength and heat resistance of metal can make complex and delicate metal-plastic products.
2. In particular, the combination of the insulating properties of resin and the electrical conductivity of metal enables the molded products to meet the basic functions of electrical products.
3、The combination of multiple inserts in advance makes the post-engineering of product unit combination more reasonable.
4、Inserts are not limited to metal, but also cloth, paper, wire, plastic, glass, wood, wire coils, electrical parts, etc.
5、For rigid molded products and flexible molded products on rubber gaskets, the complex work of arranging the sealing coils can be eliminated after the product is made by injection molding on the substrate, which makes it easier to automate the post-process assembly.
6. Since the molten material is joined to the metal insert, the gap between the metal insert can be designed to be narrower compared to the press-in molding method, and the composite product can be molded with higher reliability.
7、Select the appropriate resin and molding conditions, even for the easily deformed and broken injection molded products, the resin can be sealed and fixed.
8、Select the appropriate mold structure, insert products can also be completely sealed into the resin.
9、The combination of vertical injection molding machine and robot, insert molding device, etc. can realize the automatic injection molding processing production.
10、After the insert molding, it can also be made into injection molded products with hollow grooves after the core hole removal process.