How to reasonably select cold runner and hot runner from an economic point of view
In the injection molding process, one of the most important functions of the mold is to transport the melt from the barrel to the mold cavity. Melt conveying management has an important influence on the final quality of parts and the final success of the production line. The precise control of resin flow, pressure and temperature is very important in this process. Therefore, a more in-depth comparison of hot runner and cold runner solutions is very important for the early investment of the project and the economy of subsequent production.
The cold runner is the melt plastic flow channel processed on the parting surface of the mold. Its main purpose is to provide a channel for the molten resin to enter the mold cavity through the gate. After entering the cavity, the molten resin is cooled and hardened, ejected together with the part, and the next injection cycle starts again. The cold runner system usually has a small impact on the initial mold cost or initial capital expenditure, that is, the initial investment cost of the project will be small. They are usually used in molds with short or infrequent production runs and a low number of cavities.
With the increasing demand for injection molding output, the application of cavity mold is more and more extensive. When this happens, the cold runner will have many adverse effects on processing and cost, such as waste of runner materials. The complex cold runner system means more resin is injected into the mold, cooled and treated. The layout of the cold runner may be more complex. In order to accommodate the complex runner, the spacing between mold cavities must be larger.
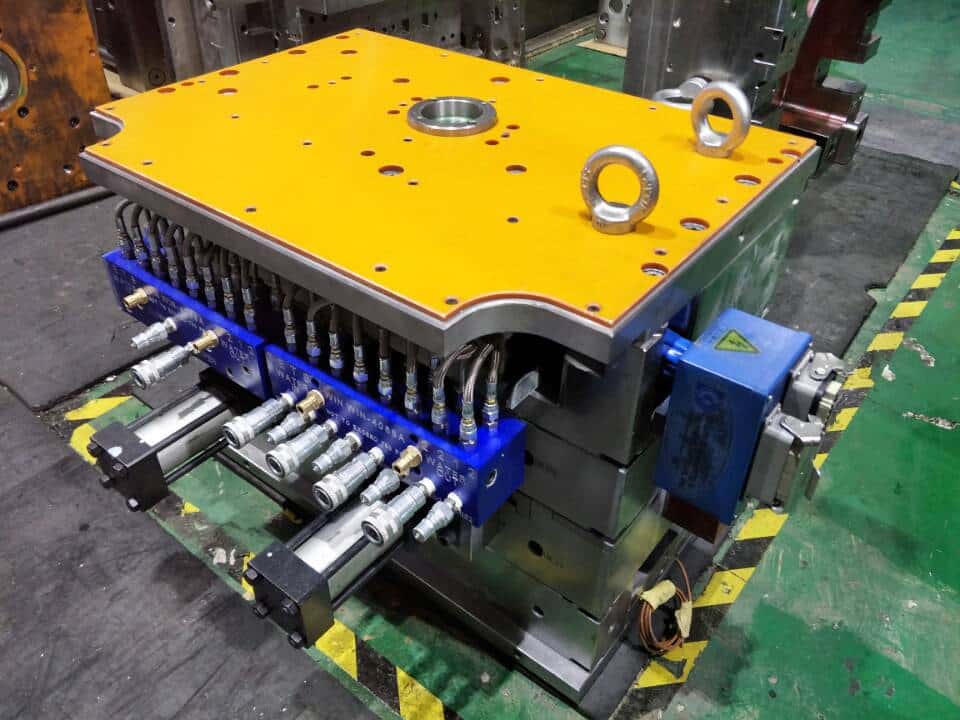
In addition, the cold runner will bring a longer cycle time, because the melt will still be filled into the cavity during the feeding phase. The thickness of the cold runner is usually greater than the thickness of the part, so it takes longer to cool the runner to ensure safe operation. In addition, the gate of the cold runner may require a larger opening stroke to be ejected smoothly, which will also extend the cycle time. When the mold is open, it takes time to remove the runner from the mold by gravity or by a manipulator. This will prolong the injection cycle time.
Hot runner
The hot runner is used to ensure that the plastic in the runner and gate remains molten by heating. Since a heating rod and a heating ring are set near or in the center of the runner, the entire runner from the nozzle outlet to the gate of the injection molding machine is in a high temperature state, so that the plastic in the runner remains molten. After shutdown, it is generally not necessary to open the runner to take out the condensate, but only need to heat the runner to the required temperature when restarting. Therefore, the hot runner process is sometimes referred to as the hot header system or the runner free molding. Its function is similar to the cold runner, because it provides a path for the molten resin to pass through a high-tech and well-designed system, and will not allow the molten resin to solidify in the runner. The melt flow channel is enclosed in a steel manifold and will not be exposed to air. The manifold distributes the molten resin to the nozzle for access to the gate and cavity. The temperature of manifold and nozzle is regulated by thermocouple and heater to keep the temperature of molten plastic consistent. In contrast, the cold runner can be compared to an open-air downtown street, while the hot runner is more like a subway tunnel
Generally speaking, the production design and manufacturing cycle of hot runner mold is longer than that of cold runner mold, involving more links, so as far as the mold cost itself is concerned, hot runner mold is much more expensive The economic advantages of hot runner mold are mainly realized by reducing and eliminating production waste and realizing injection molding production automation.
If the output of plastic products is required to be very large (such as millions of pieces) and the production rate is required to be high, the application of hot runner has great advantages Generally speaking, the most important factor affecting the injection molding cycle is the cooling and curing time of plastic products On the cold runner mold, the cooling time is longer because the cross section size of the runner system is often larger than the wall thickness of the plastic products This often leads to a longer overall injection molding cycle On the contrary, the injection molding cycle can be significantly reduced on the hot runner mold because there is no cold runner requiring a long cooling time In addition, the cold runner mold requires secondary processing operations, such as trimming the gate and recycling the waste of the runner system The application of hot runner mould can avoid the problems of secondary processing operation and realize the automation of injection molding production For projects with expensive plastic raw materials, large product output requirements and no permission to use recycled materials for processing, hot runner molds should be the preferred mold category.
When the output of plastic products is small, the proportion of mold cost in the price of plastic products is relatively high. At this time, it is more economical to choose cold runner molds. The mold delivery period is short, and the use and maintenance are relatively simple As hot runner components are expensive, and the production design and manufacturing cycle of hot runner molds is much longer than that of cold runner molds, it is not suitable to use hot runner molds for processing and molding in terms of economic cost for injection molding projects that require short, flat and fast molding, instead of cold runner molds.
Compared with cold runner mold, hot runner mold is more prone to various production failures The use and maintenance of hot runner die is relatively complicated Hot runner element devices work under high temperature and high pressure dynamic load, and many factors lead to their failure. Many hot runner components are also wearing parts, which need to be replaced regularly Therefore, hot runner users often need to purchase spare components in addition to purchasing normal hot runner systems This will increase the use cost of additional hot runner molds The cold runner mold failure is much less likely For many hot runner mold failures, the hot runner supplier often needs to send technical service personnel to help solve them These technical services are often paid services, which will increase the cost of using hot runner molds At the same time, the economic benefits of plastic injection molding process are mainly guaranteed by continuous mass production, so once there is a production stop fault, the economic loss is great Therefore, when determining whether to use cold runner or hot runner mold for injection molding processing cost accounting, it is necessary to consider whether the hot runner mold shutdown failure can successfully solve this factor
From the above discussion, we can see that there are many economic cost factors to decide whether to use hot runner mold It is necessary to consider comprehensively Generally speaking, for projects with large batch production requirements and expensive plastic raw materials, and companies with rich technical experience should consider using hot runner molds On the other hand, for projects with small production volume, insufficient technical experience of users and general product quality requirements, it is more economical to use traditional cold runner molds