Injection Molding Process Characteristics of Transparent Raw Materials
The injection molding process characteristics of transparent plastics are described as follows:
1. PMMA has high viscosity and poor fluidity, so it must be injected with high material temperature and injection pressure. The influence of injection temperature is greater than that of injection pressure, but the increase of injection pressure is conducive to improving the shrinkage of the product.
The injection temperature range is wide, the melting temperature is 160 โ, and the decomposition temperature is 270 โ, so the material temperature adjustment range is wide and the processability is good. Therefore, the improvement of fluidity can be started from the injection temperature. Poor impact, poor wear resistance, easy to scratch, easy to crack, so we should improve the mold temperature, improve the condensation process to overcome these defects.
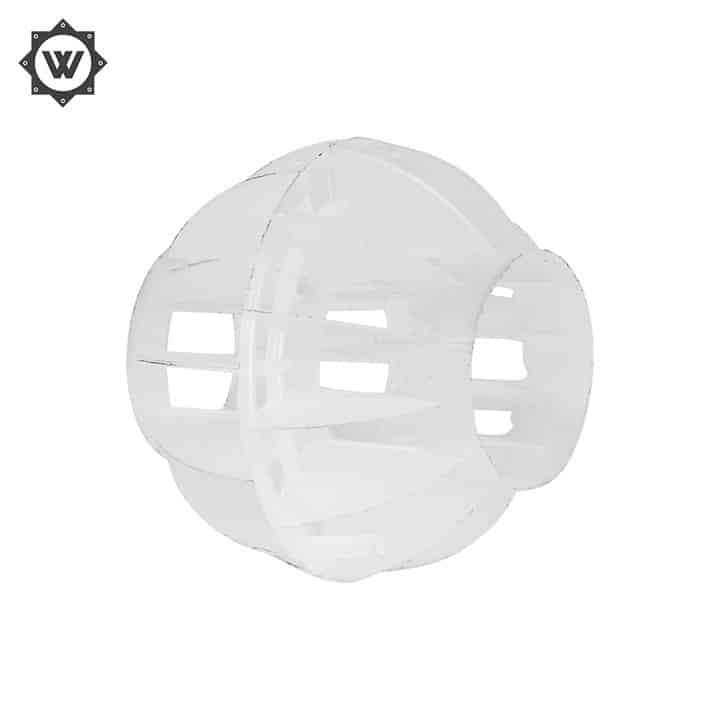
2. PC has high viscosity, high melting temperature and poor fluidity, so it must be injected at a higher temperature (270
– 320T), the range of material temperature adjustment is relatively narrow, and the processability is not as good as PMMA. The injection pressure has little effect on the fluidity, but the injection pressure is still high due to the high viscosity. In order to prevent the generation of internal stress, the pressure holding time should be as short as possible.
The shrinkage rate is large and the size is stable, but the internal stress of the product is large and easy to crack, so it is better to improve the fluidity by increasing the temperature rather than the pressure, and reduce the possibility of cracking by increasing the mold temperature, improving the mold structure and post-treatment. When the injection speed is low, ripples and other defects are easily generated at the gate. The temperature of the radiation nozzle should be controlled separately, the mold temperature should be high, and the resistance of the runner and gate should be small.
3. PET has a high molding temperature and a narrow range of material temperature adjustment (260-300 โ), but after melting, it has good fluidity, so its processability is poor. In addition, an anti flow device is often required in the nozzle. The mechanical strength and performance are not high after injection, and the performance can only be improved through stretching process and modification. The mold temperature is accurately controlled to prevent warping. Therefore, it is recommended to use hot runner die. The mold temperature is high, otherwise it will cause poor surface gloss and difficult demoulding.