Injection Molds and Hot Runners
Injection molds are composed of several steel plates with various parts, basically divided into.
A Forming device (concave die, convex die)
B positioning device (guide pillar, guide sleeve)
C fixture (I-plate, mold pit)
D cooling system (water transport hole) E thermostatic system (heating tube, hot wire)
F runner system (chirp hole, runner slot, runner hole)
G Ejector system (ejector pin, ejector stick)
According to the different types of casting system can be divided into three types of molds.
1、Large spout molds: runner and gate are on the parting line, and the product is demolded together when the mold is opened, the design is the simplest, easy to process and low cost, so more people use large spout system for operation.
2, fine spout mold: runners and gates are not on the parting line, generally directly on the product, so to design more than one group of spout parting line, the design is more complex, processing is more difficult, generally depending on the product requirements and choose fine spout system.
3, hot runner mold: this kind of mold structure and fine water mouth is largely the same, the biggest difference is that the runner is in one or more constant temperature hot runner plate and hot water mouth, no cold material demold, runner and gate directly on the product, so the runner does not need to demold, this system is also called no water mouth system, can save raw materials, suitable for raw materials are more expensive, products require higher situation, design and processing difficulties, mold cost Higher cost.
Hot runner system, also known as hot sprue system, mainly consists of hot sprue sleeve, hot sprue plate and temperature control electric box. Our common hot runner system has two forms: single point hot gate and multi-point hot gate. Single point hot gate is to use single hot gate sleeve to shoot molten plastic into the cavity directly, it is suitable for single cavity single gate plastic mold; multi-point hot gate is to branch the molten material into each sub hot gate sleeve and then into the cavity through the hot gate plate, it is suitable for single cavity multi-point feeding or multi-cavity mold.
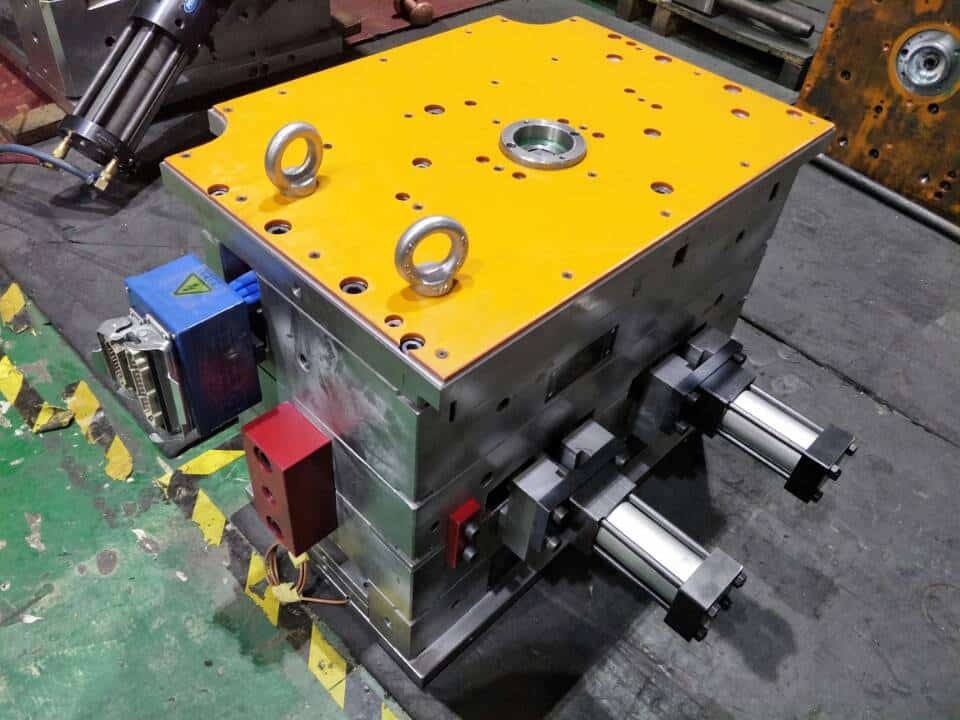
Advantages of hot runner system
1、No sprues, no post-processing, so that the whole molding process is fully automated, saving working time and improving working efficiency.
2、Small pressure loss. The hot runner temperature is equal to the injection machine nozzle temperature, which avoids the surface condensation of raw materials in the sprue, and the injection pressure loss is small.
3、The repeated use of sprues will degrade the plastic performance, while using hot runner system without sprues can reduce the loss of raw materials, thus reducing the product cost. Uniform temperature and pressure in the cavity, low stress of plastic parts, uniform density, and better injection molding than general injection molding system in a shorter molding time under a smaller injection pressure. For transparent parts, thin parts, large plastic parts or high requirements of plastic parts can show its advantages, and can use a smaller model to produce larger products.
4、The heat nozzle adopts standardized and serialized design, with various optional nozzle heads and good interchangeability. The unique design and processing of electric heating ring can achieve uniform heating temperature and long service life. The hot runner system is equipped with hot runner plates, temperature controllers, etc., with exquisite design, various types, easy to use, stable and reliable quality.
Shortcomings of hot runner system application
1、The overall mold closing height increases, because of the addition of hot runner plate, etc., the overall height of the mold increases.
2、It is difficult to control the heat radiation, the biggest fault of hot runner is the heat loss of the sprue, which is a major issue to be solved.
3、There is thermal expansion, thermal expansion and contraction is a problem to be considered when we design.
4、The cost of mold manufacturing increases, the price of standard parts of hot runner system is high, which affects the popularity of hot runner mold.
The advantages of hot runner mould
Hot runner molds are extremely widely used in all industrial developed countries and regions in the world today.
This is mainly because hot runner molds have the following significant features.
1, shorten the molding cycle of the parts because there is no sprue system cooling time limit, the parts molding curing can be timely ejected. Many thin-walled parts produced with hot runner molds can be molded in less than 5 seconds. This is particularly significant for applications where plastics are expensive. In fact, the major international hot runner manufacturers have experienced rapid growth in the world when oil and plastic materials were expensive. Because hot runner technology is an effective way to reduce the cost of materials to reduce material costs.
2、Reduce the cost of products, improve product quality in the hot runner mold molding process, the plastic melt temperature in the runner system to get accurate control. The plastic can flow into each mold cavity in a more uniform state, and the result is consistent quality parts. Hot runner molded parts have good gate quality, low residual stress after release, and low part distortion. So many high quality products in the market are produced by hot runner molds. Such as familiar MOTOROLA cell phones, HP printers, DELL notebook computers in many plastic parts are made by hot runner molds
3、Eliminate the follow-up process, which is conducive to production automation. The parts are finished after being molded by hot runner mold, no need to trim the gate and recycling process such as cold sprue. It is conducive to production automation. Many foreign product manufacturers are hot runner and automation combined to significantly improve production efficiency.
4, expand the application of injection molding process from many advanced plastic molding process is based on the development of hot runner technology. Such as PET preform production, in the mold of multi-color co-injection, a variety of materials co-injection process, STACK MOLD, etc..
Disadvantages of Hot Runner Molds
Although hot runner molds have many significant advantages over cold runner molds, mold users also need to understand the disadvantages of hot runner molds. In summary, there are the following points.
1, mold cost increases
Hot runner components are more expensive, and the cost of hot runner molds may increase significantly. If the part production is small, the mold tooling cost ratio is high, the economy is not spent on calculations. For many developing countries mold users, hot runner system price is expensive is one of the main problems affecting the widespread use of hot runner mold.
2, hot runner mold production process equipment requirements high
Hot runner mold need precision processing machinery for guarantee. Hot runner system and mold integration and cooperation requirements are extremely strict, otherwise the mold in the production process will have many serious problems. Such as bad plastic sealing lead to plastic overflow damage hot runner components to interrupt production, nozzle insert and gate relative position is not good to lead to serious decline in product quality, etc..
3、Complex operation and maintenance
Compared with the cold runner mold, hot runner mold operation and maintenance is complicated. Such as the use of improper operation is very easy to damage the hot runner parts, so that the production can not be carried out, resulting in huge economic losses. For new users of hot runner molds, it takes a long time to accumulate experience.
The composition of the hot runner system
Although there are many hot runner manufacturers in the world and a variety of hot runner product line, but a typical hot runner system are composed of the following major components.
1、Hot runner plate
2、Nozzle
3、Temperature controller
4、Auxiliary parts
Hot runner application main technology key
A successful hot runner mold application project requires several aspects to be guaranteed. Among them, there are two most important technical factors.
One is the control of plastic temperature, and the other is the control of plastic flow.
1, the control of plastic temperature in the hot runner mold application of plastic temperature control is extremely important.
Many production process and product quality problems arise directly from the hot runner system temperature control is not good. Such as the use of hot needle gate method injection molding when the product gate quality is poor, valve gate method molding valve pin closure difficulties, multi-cavity mold parts filling time and quality inconsistent problems. If possible, you should try to choose a hot runner system with multiple regions to control temperature separately to increase the flexibility and adaptability.
2, the plastic flow control
Plastic in the hot runner system to flow balance. The gate should be opened at the same time so that the plastic synchronously fill the cavities. FAMILYMOLD for parts with significant differences in weight to balance the sprue size design. Otherwise, some parts will not have enough mold pressure and some parts will have too much mold pressure and poor quality of flying edges. Hot runner sprue size design should be reasonable. Size is too small mold filling pressure loss is too large.
Size is too large, the hot runner volume is too large, plastic in the hot runner system for too long, damage to material properties and lead to parts can not meet the requirements of use after molding. CAE software such as MOLDCAE is already available worldwide to help users with optimal runner design.