Precautions before mold test of injection mold
1. Understand the relevant information of the mold
It is better to obtain the design drawing of the mold, make a detailed analysis, and invite the mold technician to participate in the mold test.
2. Check the mechanical cooperation action on the workbench
Attention shall be paid to whether there are scratches, missing parts, looseness, etc., whether the action of the die sliding plate is accurate, whether there is leakage in the water channel and gas pipe joints, and if there is a limit to the opening of the mold, it shall also be marked on the mold. If the above actions can be done before hanging the mold, it can avoid the waste of working hours caused by finding problems during hanging the mold and then disassembling the mold.
3. When it is determined that each part of the mold acts properly, it is necessary to select a suitable mold testing injection molding machine. Attention shall be paid to:
(1) What is the maximum injection rate of the injection molding machine;
(2) Whether the inner distance of pull rod can place the mold;
(3) Whether the maximum movement stroke of movable formwork meets the requirements;
(4) Whether other tools and accessories for mold testing are complete.
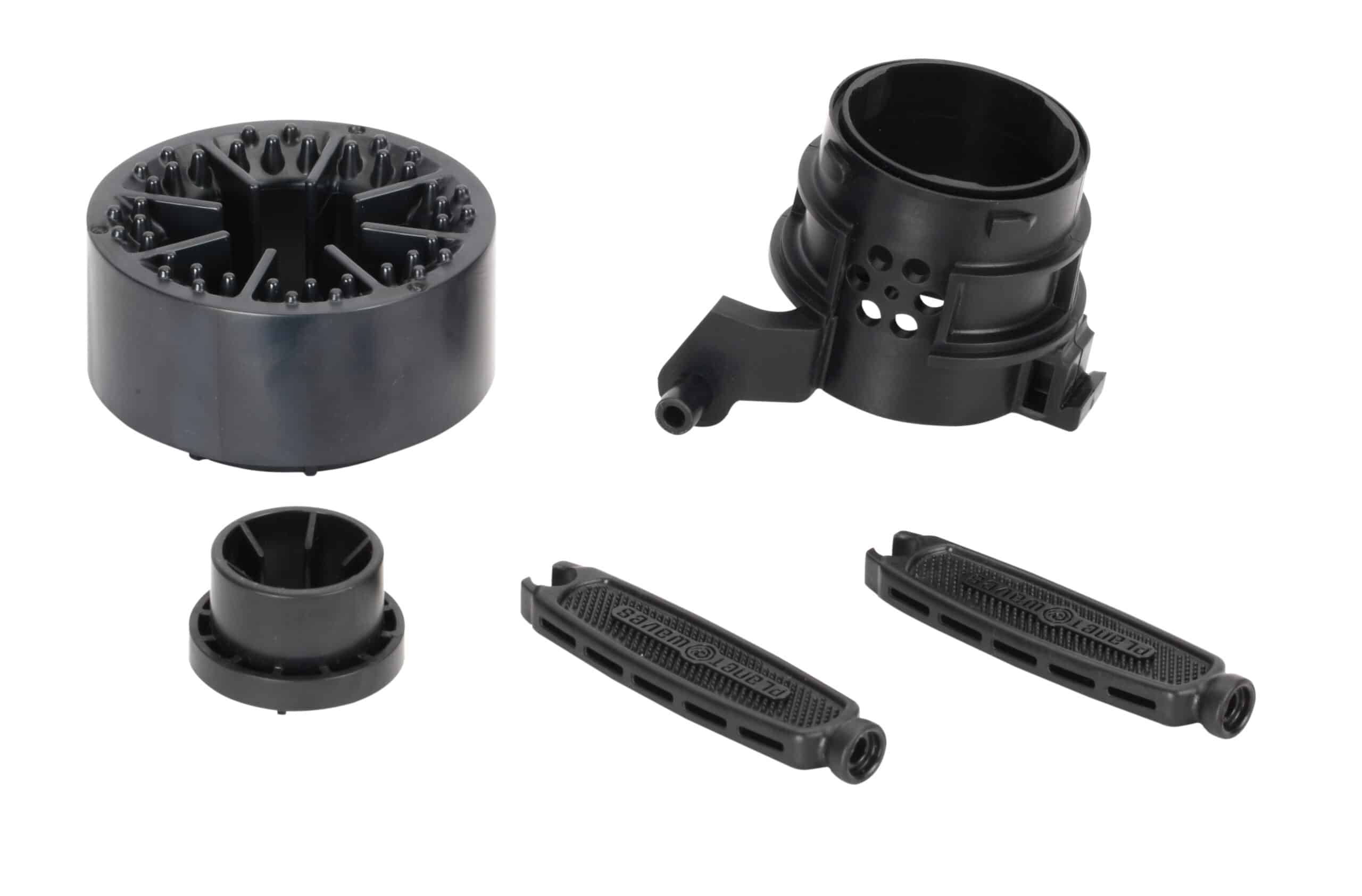
After everything is confirmed to be OK, the next step is to hang the mold. During hanging, it shall be noted that the hook shall not be taken down before locking all clamping templates and opening the mold, so as to avoid loosening or fracture of clamping templates and falling of the mold.
After the mold is installed, carefully check whether the mechanical actions of all parts of the mold, such as sliding plate, ejector pin, tooth withdrawing structure and limit switch, are correct, and pay attention to whether the injection nozzle is aligned with the feed inlet.
The next step is to pay attention to the mold closing action. At this time, the mold closing pressure should be lowered. During the manual and low-speed mold closing action, pay attention to whether there is any unsmooth action or abnormal sound. In fact, the process of lifting the mold is relatively simple. The main thing that needs to be careful is that it is difficult to adjust the center of the mold gate and the nozzle. Usually, the test paper can be used to adjust the center.
4. Increase mold temperature
According to the properties of raw materials used for products and the size of the mold, appropriate mold temperature controller is selected to raise the mold temperature to the temperature required for production. After the mold temperature is raised, the action of each part must be checked again, because the steel may cause clamping phenomenon due to thermal expansion, so pay attention to the sliding of each part to avoid strain and vibration.
5. If the factory does not implement the experimental planning rule, it is suggested that only one condition can be adjusted at a time when adjusting the mold test conditions, so as to distinguish the impact of a single condition change on the products.
6. Bake the raw materials properly according to the different raw materials.
7. Try to use the same raw materials as far as possible for mold testing and future mass production.
8. Do not completely test the mold with inferior materials. If there is a need for color, color test can be arranged together.
9. Internal stress and other problems often affect secondary processing. After the mold test, the mold shall be processed again when the product is stable. After closing slowly, adjust the clamping pressure and operate it several times to check whether the clamping pressure is uneven, so as to avoid burrs and mold deformation.
After the above steps have been checked, the mold closing speed and pressure shall be lowered, the safety catch bar and jacking travel shall be set, and the normal mold closing speed and mold closing speed shall be adjusted. If the limit switch of the maximum stroke is involved, the mold opening stroke shall be adjusted a little short, and the high-speed mold opening action shall be cut off before the maximum mold opening stroke. This is because the high-speed action travel is longer than the low-speed one in the whole mold opening travel during mold installation. On the plastic machine, the mechanical ejector rod must also be adjusted to function after the full speed mold opening action, so as to avoid the deformation of the ejector pin plate or stripping plate due to force.
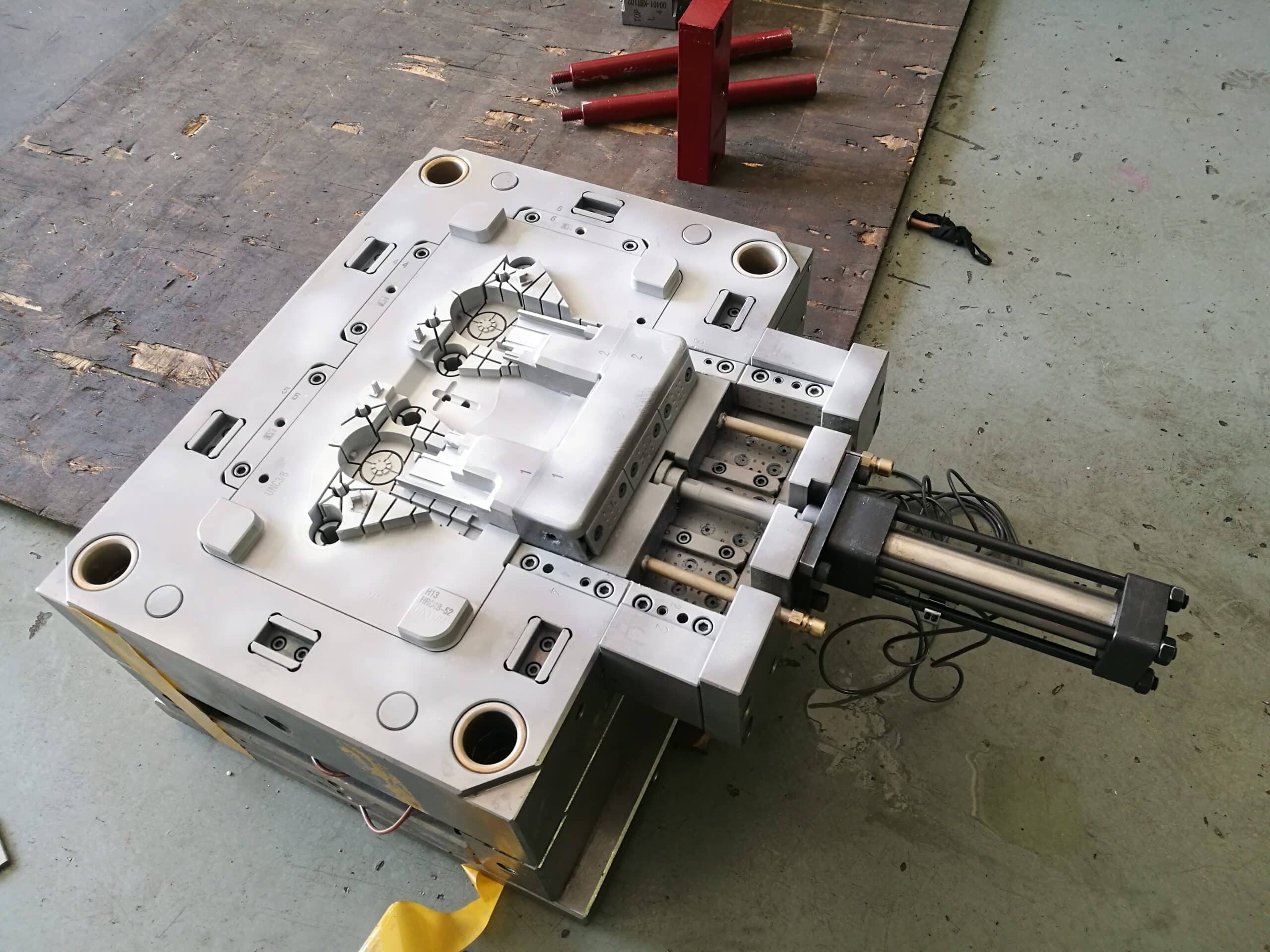
Please check the following items before making the first injection:
inspect
(1) Whether the feeding stroke is too long or insufficient;
(2) Whether the pressure is too high or too low;
(3) Whether the filling speed is too fast or too slow;
(4) Whether the processing cycle is too long or too short.
To prevent short shot, fracture, deformation, burrs and even damage to the mold. If the processing cycle is too short, the thimble will puncture the product or peel the ring to crush the product, which may take you two or three hours to take out the product. If the processing cycle is too long, the thin and weak parts of the mold core may be broken due to the rubber material shrinkage. Of course, you can’t anticipate all possible problems in the process of mold trial, but it will help you avoid serious and expensive losses if you fully consider and take timely measures in advance.