The application of new injection molding technology in injection molding processing, although there are many similarities between the injection molding principles and processes of thermosetting and thermoplastic plastics, there are also great differences between them due to their different chemical properties. The injection principle of thermosetting plastics is to heat the molding materials from the hopper of the injection machine into the barrel and melt and plasticize them under the rotating action of the screw, so that they can become uniform viscous liquid melts. Driven by the high pressure of the screw, these melts can be injected into the high-temperature cavity at a large flow rate through the nozzle at the front end of the barrel. After a period of pressure maintaining, feeding and cross-linking reaction, they can be solidified into plastic shapes, Then open the mold and take out the plastic part. It is obvious that in principle, the main difference between thermosetting and thermoplastic injection molding is in the curing stage after the melt is injected into the mold. The curing of thermoplastic injection molded parts is basically a physical process of transition from high temperature liquid phase to low temperature solid phase, while the curing of thermosetting injection molded parts must depend on the cross-linking chemical reaction under high temperature and high pressure. It is precisely because of this difference that the injection molding processing conditions of the two are different.
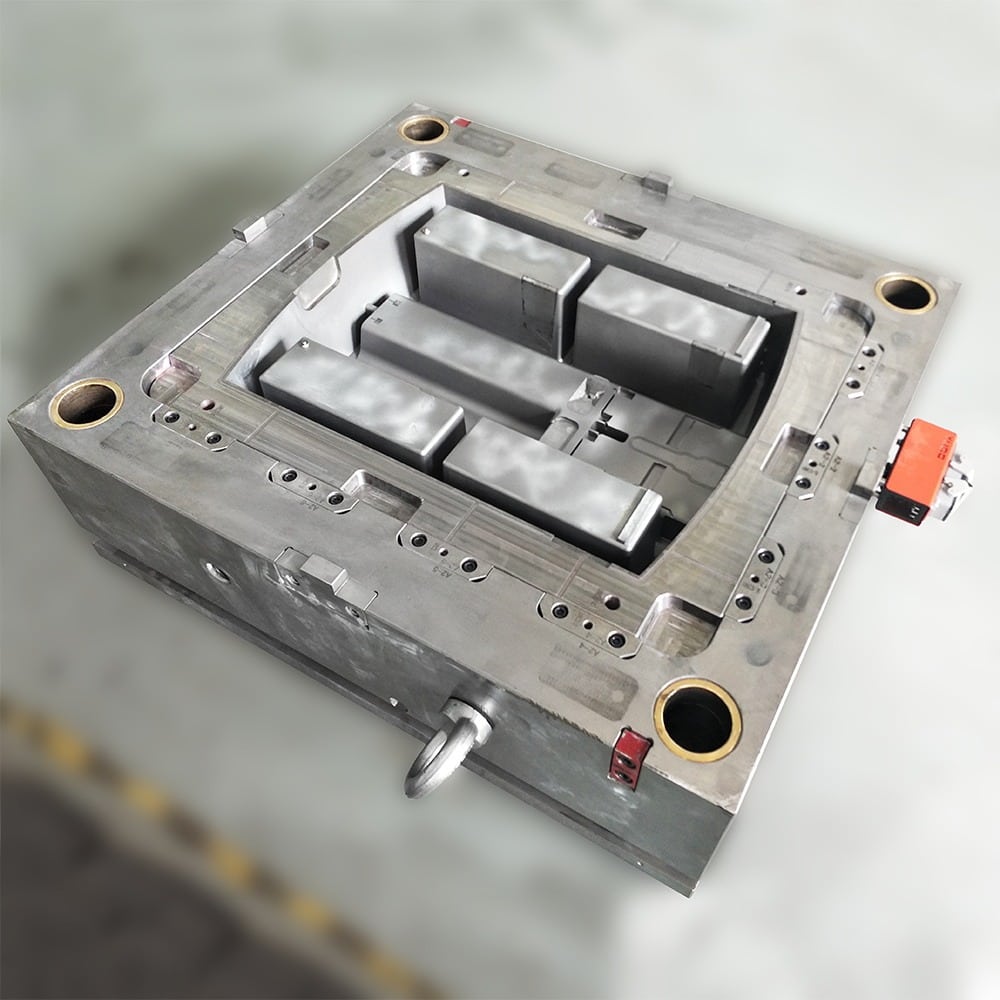
Precautions for injection mold processing:
1. The required raw materials can be dried for 2 hours at 80 ℃ if necessary.
2. The forming temperature range is large, and the heating, melting and curing speed are fast, so the forming cycle is relatively short.
3. The mold temperature shall be controlled at 50-80 ℃.
4. GPPS has good fluidity and does not need high pressure in beer molding, so as not to increase the internal stress of rubber parts due to excessive pressure, which will lead to cracking.
5. The injection speed will be affected by the injection working pressure. If the speed is too fast, it will lead to some problems such as flaring, sticking when the mold is out, and white crack when the mold is ejected.