the benefits of laser heat treatment for automotive molds
Compared to U.S. OEMs, for the exact same automotive tooling, automotive tooling OEMs across Europe are delivering it faster, with higher quality and at a lower cost. The reason for this is laser heat treating (see Figure 1), a process that is close to mainstream in Europe, but hardly ever practiced in the United States.
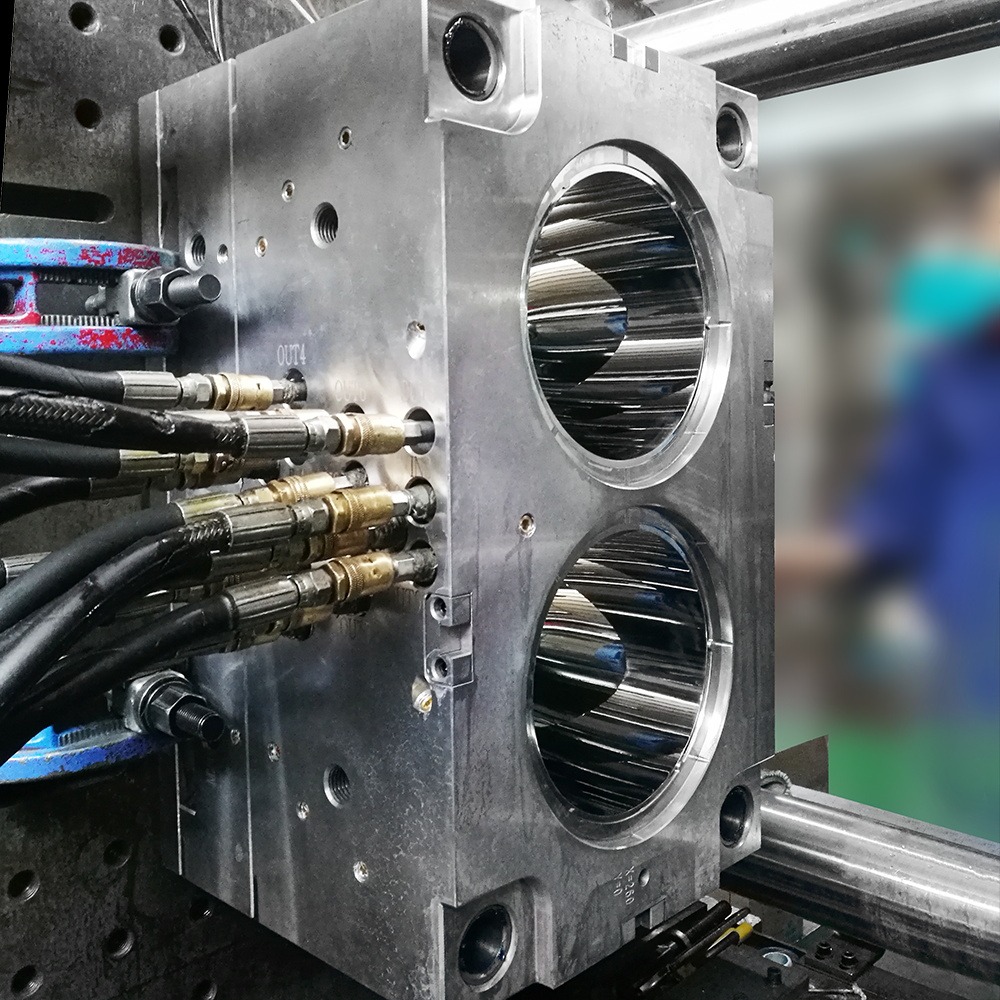
Laser heat treating has been universally successful in Europe, and adoption of the technology by U.S. OEMs was a given. Barriers to the acceptance of laser heat treating by U.S. automotive mold OEMs include the fact that this technology is still not well understood in the United States. Data on the cost savings, quality and schedule improvements of laser heat treating have not yet been transferred to U.S. decision makers; and there are few reliable laser heat treating process shops in the United States. However, it is clear that laser heat treating is expected to be rapidly adopted within the U.S. OEM industry.
What is laser heat treating?
In the laser heat treating process, a laser beam with typical spot sizes between 0.5 x 0.5 inches and 2 x 2 inches is directed at the surface of a metal part as a means of delivering heat to it. Laser energy is delivered in such a way as to raise the temperature of the metal surface and heat affected zone (HAZ) above its metallurgical transition temperature. When the laser heat source is removed, the heat of the metal is removed by conduction heat to provide rapid quenching of the heated zone, resulting in the desired hardness. The details of the laser beam operation can be finely tuned to provide precise control of all aspects of the hardening process. Depending on the geometry, laser heat treatment also allows areas that are difficult to reach by other means to be treated by line-of-sight. Laser heat treatment is sometimes referred to as laser hardening.
Benefits of laser heat treatment
The benefits of laser heat treatment compared to traditional heat treatment techniques such as induction, furnace and flame heat treatment are
Consistent depth of hardness By precisely controlling the energy delivered to the metal itself, including millisecond feedback control, the nature of the laser energy means that laser heat treating can produce tightly-specified HAZs, resulting in a consistent depth of hardness within very tight tolerances.
Most automotive molds do not require hard milling In addition to the precise control mentioned earlier, the inherent nature of the laser energy itself means that for any given HAZ size, laser heat treating can automatically deliver the smallest possible total energy to the mold being treated. In most automotive molds, the process has a built-in feature that automatically achieves zero distortion. Unlike conventional heat treatment methods that require grinding additional material after the heat treatment, laser heat treatment is performed after the mold has been cut into its final shape. This saves costs by avoiding additional machining operations when the material is hard.