What are the characteristics of the appearance design of injection moulds?
Appearance design can leave a deep impression, consumers can’t see the internal quality of the product, but they can observe whether the product’s appearance design is smooth and the process quality is good, and then do a good job of overall accurate positioning of the product, such as appearance design is not standard, it may lead to the injection mold completely scrapped, so be especially careful. Appearance design requires a beautiful and generous product design, smooth surface connection, natural, most of the electronic devices used in real life, the shell mainly consists of the upper and lower shell, but in fact, due to the injection mold manufacturing precision, injection parameters and other factors, resulting in inconsistent size of the upper and lower appearance, that is, the surface scraping (shell is larger than the bottom shell) or bottom scraping (bottom shell is larger than the shell).
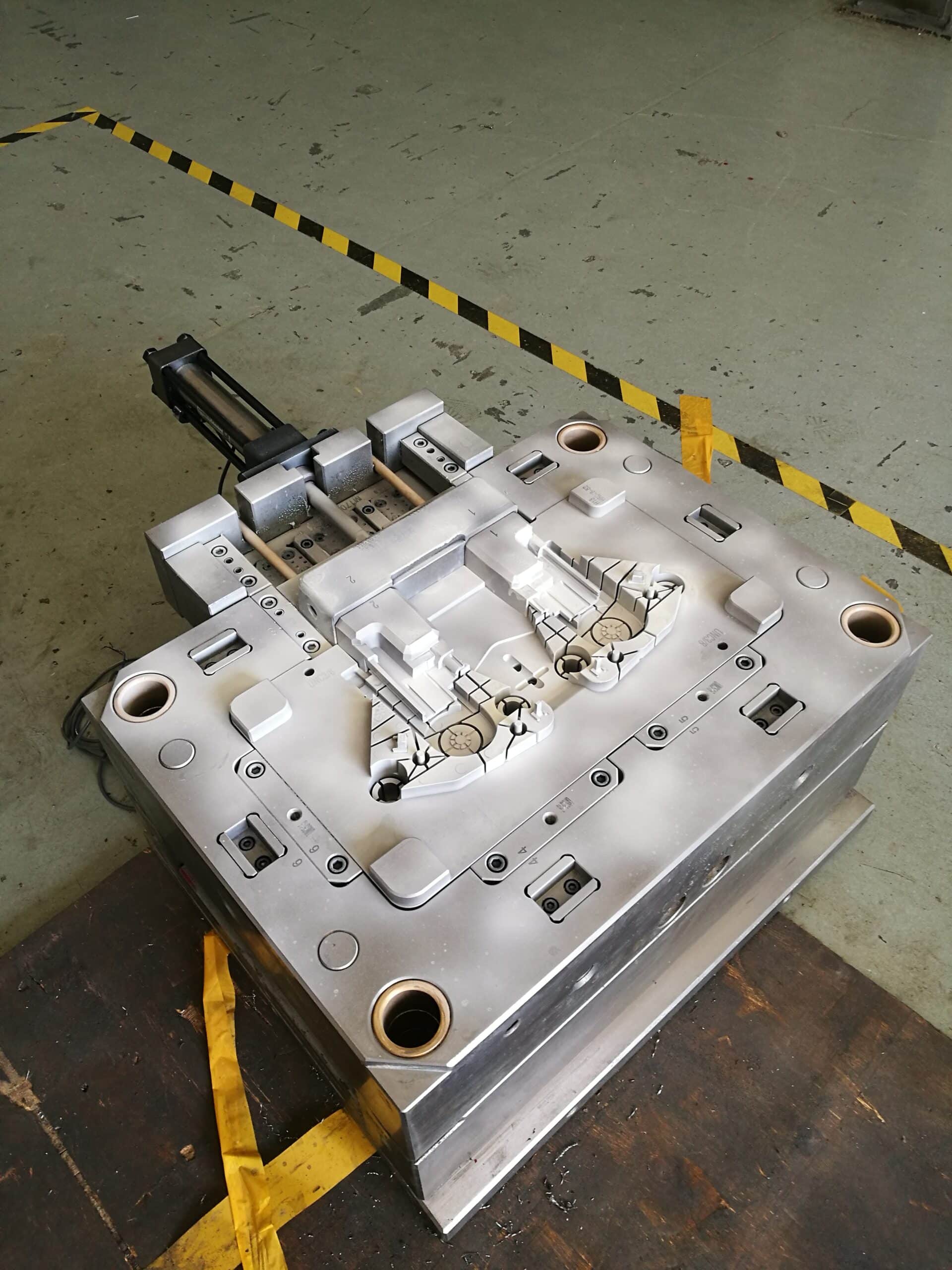
A, the appearance of the design of common plastic introduction
In the appearance design, the choice of materials selected will directly affect the shape of the product. The selected materials are different, the quality of the process and the process is also different. Some selected materials are difficult to withstand too much bending and construction. If the selected materials are not chosen in a standard way, there is no way to make the ultimate shape and achieve the desired effect.
The appearance of the product must be designed with attention to stability. Designers usually lower the physical and visual center of gravity of the product by strengthening, widening and weighting the chassis, thus making the product more stable, safe and reliable.
Commonly used plastic materials are mainly ABS, AS, PC, PMMA, PS, HIPS, PP, POM, etc., where the commonly used transparent plastic PC, PMMA, PS, AS. generally choose high-grade electronic equipment shell ABS + PC; display selected PC, such as the choice of PMMA to do a good job of surface hardening treatment. The bottom of the electronic equipment is mainly used in the case HIPS and ABS to do the case.
Second, the appearance of the design of common surface treatment introduced
Surface treatment using electroplating process, electrostatic spraying, screen printing ink, pad printing. ABS, HIPS, PC materials have good surface treatment of the actual effect. And PP material surface treatment performance is poor, generally using pre-treatment process.
Third, the appearance design to meet the requirements of the film release
Product appearance design must have feasibility analysis and real landing, through a variety of processes to integrate the art of modeling into the production of industrial products can be produced to ensure that the design products can be produced, is a real product design.
No matter how extreme the design is, if it is not practical, there is no way to accomplish real landing production, it is just meaningless talk with no use value.
Plastic products are generally made by heating the plastic in a viscous flow state, molding cooling and hardening, should ensure sufficient decoupling slope, otherwise the plastic parts are difficult to decoupling, forced decoring, which generally leads to plastic parts distortion, product design surface strains, white or cracking, etc.. Otherwise, it will lead to cavity deflection, resulting in poor delamination.