What injection molding process parameters need to be adjusted to solve the stress problem?
In the molding process of plastic products, any molding factors that can reduce the molecular orientation of the polymer in the product may reduce the orientation stress; but any process conditions that can make the polymer in the product evenly cooled can reduce the cooling internal stress; any processing methods that help plastic products to release from the mold are conducive to reducing the release internal stress.
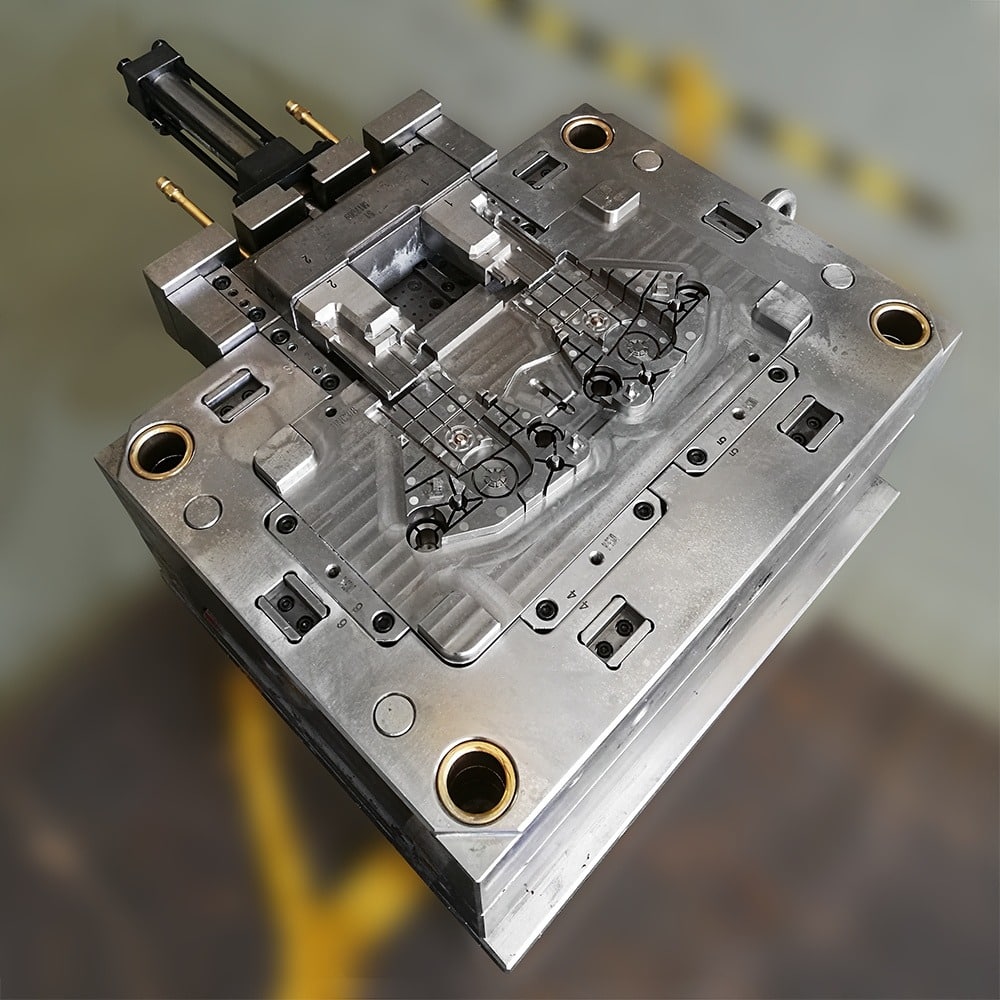
The main processing conditions that have a significant impact on internal stress are as follows.
โ Barrel temperature
Higher barrel temperature is conducive to the reduction of orientation stress, because in higher barrel temperature, the melt plasticization uniformity, viscosity decline, mobility increase, in the process of melt filling the cavity, molecular orientation is small, and therefore orientation stress is small.
In the lower barrel temperature, the melt viscosity is higher, the molecular orientation is more in the process of filling the mold, and the residual internal stress is larger after cooling and shaping. However, too high barrel temperature is not good, too high is easy to cause insufficient cooling, easy to cause deformation when demoulding, although the orientation stress is reduced, but cooling stress and demoulding stress increased.
โกMold temperature
The temperature of the mold has a great influence on the orientation stress and cooling stress. On the one hand, the mold temperature is too low, it will cause the cooling to accelerate, easy to make the cooling uneven and cause large differences in shrinkage, thus increasing the cooling stress.
On the other hand, the mold temperature is too low, the melt into the mold after the temperature drop faster, the melt viscosity increases rapidly, resulting in high viscosity under the filling of the mold, the formation of the degree of orientation stress significantly increased.
The higher the mold temperature, the more conducive to grain stacking tightly, the internal shortcomings of the crystal is reduced or eliminated, thereby reducing internal stress.
In addition, for different thickness of plastic products, the mold temperature request is different. For thick-walled products, the mold temperature should be appropriately high.
โขInjection pressure
Injection pressure is high, the melt filling process is subjected to shear force, the opportunity to produce orientation stress is also greater. Therefore, in order to reduce the orientation stress and eliminate the release stress, the injection pressure should be properly reduced.
โฃPressure holding pressure
The impact of holding pressure on the internal stress of plastic products is greater than the impact of injection pressure. In the pressure-holding stage, the melt temperature decreases, and the melt viscosity increases rapidly, which will lead to the forced orientation of the molecular chains if high pressure is applied, resulting in greater orientation stress.
โค Injection speed
The faster the injection speed, the easier it is to cause the degree of orientation of the molecular chain to increase, thus causing greater orientation stress. However, if the injection speed is too low, the plastic melt may be layered into the mold cavity and melt marks may be formed, resulting in stress concentration lines and stress cracking.
Therefore, the injection speed should be moderate. It is better to use variable speed injection and stop filling the mold when the speed decreases gradually.
โฅPressure-holding time
The longer the holding time, it will increase the shearing effect of the plastic melt, thus producing greater elastic deformation and freezing more orientation stress. Therefore, the orientation stress increases significantly with the increase of the holding time and the growth of the amount of replenishment.
(7) Residual pressure of mold opening
The injection pressure and holding time should be adjusted appropriately so that the residual pressure in the mold is close to the atmospheric pressure when the mold is opened, thus avoiding greater internal stresses in the mold release.