What is the injection molding process and principle?
The basic principle of injection molding is to add granular or powdery raw materials to the hopper of the injection molding machine. The raw materials are melted and become liquid after heating. Promoted by the screw rod or piston rod of the injection molding machine, the raw materials enter the shell mold through the injection nozzle and the gating system software of the die-casting mold, and the mold mold is hardened and shaped.
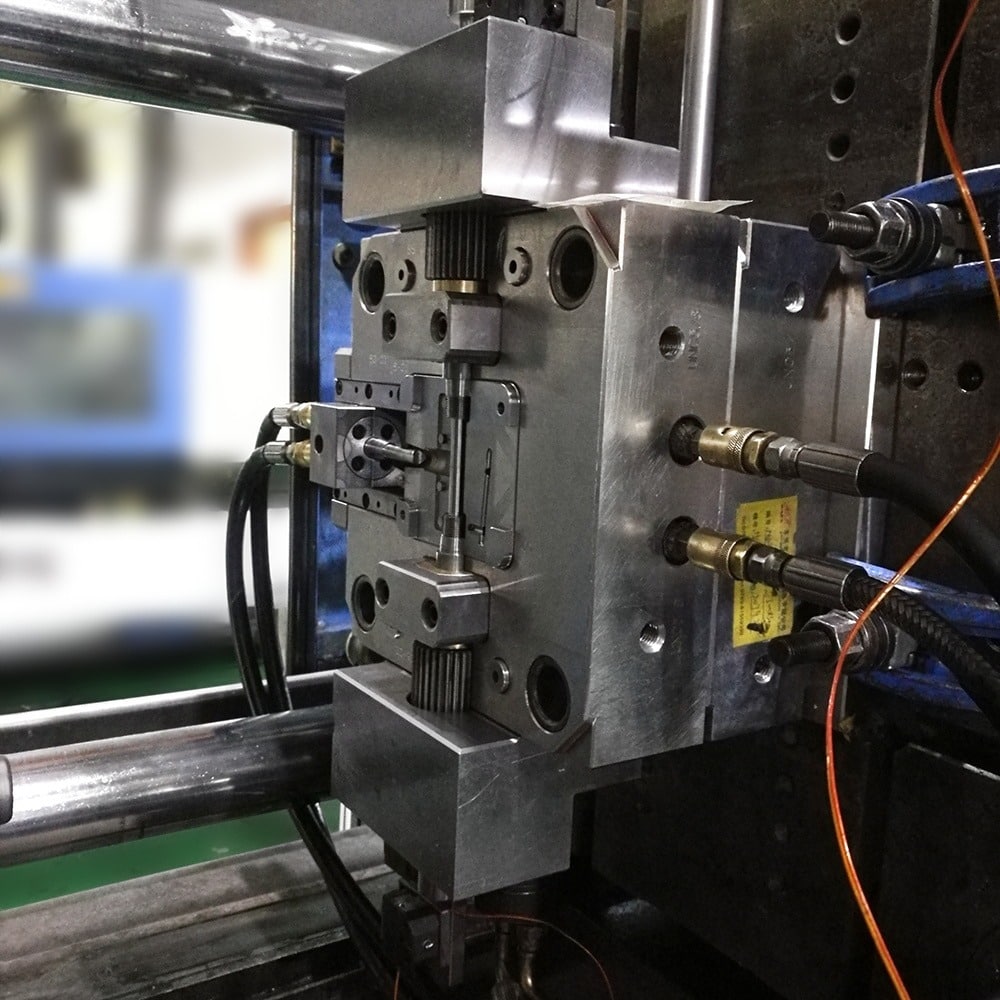
Injection molding processing must meet two necessary conditions for molding: the plastic must be injected into the cavity of the injection mold in a molten state, and the injected plastic melt must have sufficient pressure and flow speed to fully fill the cavity of the mold. Therefore, injection molding must have the basic functions of plastic plasticization, melt injection molding and pressure retaining molding.
Plastic plasticizing: During the plasticizing process of injection molding, solid plastic continuously moves forward along the direction of the screw groove through the conveying action of the rotating screw. After heating, compaction, shearing and mixing of the screw threads, it heats up and transforms into a viscous plastic melt with uniform density, viscosity, composition and stable distribution.
Injection molding process: The plasticized plastic melt is stored in the material storage area of the barrel. During injection molding, the screw moves axially. Under the effect of the screw injection pressure, the plastic melt has a certain rate of flow through the nozzle installed in the front section of the barrel, the mold gating system, etc. and is injected into the mold cavity of the mold.
Cooling and shaping process of injection molding: the plastic melt injected into the mold cavity overcomes various flow resistances and fills the mold cavity. The plastic melt filled with the mold cavity is subjected to huge pressure from the mold cavity, which tends to drive the plastic melt back to the barrel. The cooling effect of the mold cavity makes the plastic melt cool and shrink. At this time, the injection screw continues to provide pressure to keep the plastic melt full of the mold cavity without backflow, The plastic melt shall be properly added to the mold cavity to fill the shrinkage space in the mold cavity until the plastic melt is gradually cooled and solidified into products.
Factors affecting the quality of injection molding process: introduction of working pressure, injection molding processing time, and injection molding processing environment temperature. It uses the thermochemical properties of plastics to add raw materials from the silo to the cylinder, and the material is heated by an electric heating coil outside the cylinder to melt the raw materials. The cylinder is equipped with a screw rod which is pushed by an external driving force motor.
Under the effect of the screw rod, the raw materials are transported forward along the screw groove and compacted. The raw materials are slowly melted, melted and homogenized under the multiple functions of heating and cutting the screw rod. When the screw rod rotates, the raw materials are pushed down the top of the screw rod under the effect of sliding friction and shear stress of the screw groove.
The screw rod reverses under the reaction force of raw materials, so that the top of the screw rod forms the space in the blanking chamber, and the whole melting process is carried out. Then, the screw rod, under the effect of the driving force of the piston rod injected into the hydraulic cylinder, injects the molten material in the blanking chamber into the female mold of the mold shell according to the nozzle with rapid and high pressure.